Introduction: The Hidden Energy Crisis in Manufacturing
In the high-paced world of industrial manufacturing, energy is both a lifeline and a financial burden. Every kilowatt counts, yet most factories operate blindly—reacting to problems rather than preventing them. With the Energy Efficiency and Conservation Act (EECA) 2024 looming, energy managers across Malaysia are scrambling to improve efficiency, meet compliance requirements, and prove return on investment (ROI) for energy-saving projects.
This case study examines a Penang-based consumer electronics manufacturing plant that faced escalating energy costs, compliance pressures, and a flood of vendors promising savings—but without a way to verify results. Could real-time energy monitoring be the game-changer they needed?
Disclaimer: This case study is a hypothetical scenario based on specific conditions and challenges commonly faced by manufacturing plants. The solutions and results described are illustrative and may vary depending on individual circumstances.
The Problem: A Chaotic Energy Landscape
Mr. Lim, the plant’s Engineering Manager cum Energy Manager, faced an overwhelming challenge daily. His department, already stretched thin managing production efficiency, now had an additional KPI—energy management. With no dedicated energy specialist and HR indicating that hiring would take at least 18 months due to budget and approval constraints, Mr. Lim and his team had to take on this massive responsibility, despite their already heavy workload.
1. The Struggle of Balancing Responsibilities
Juggling energy management while ensuring production uptime meant Mr. Lim was often caught in back-to-back meetings, firefighting operational issues while trying to make sense of escalating energy costs. His inbox was flooded with vendor proposals, compliance requests, and urgent inquiries from top management questioning energy expenditures.
His team was constantly asked to justify costs, prepare reports for EECA compliance, and troubleshoot unexpected power spikes. But how could they track inefficiencies without real-time insights?
“I felt like I was constantly putting out fires,” Mr. Lim shared. “We were expected to meet energy KPIs, but we didn’t even have the tools to understand where the problems were. It was frustrating.”
2. Surging Energy Costs with No Clear Cause
Despite installing a solar PV system, the plant’s monthly TNB (Tenaga Nasional Berhad) bill kept rising. The CFO, increasingly frustrated, demanded answers:
- “We invested in solar—why are we still paying more?”
- “Are our chillers, compressors, or HVAC systems running inefficiently?”
- “How do we even know where the waste is happening?”
The solar panels were generating energy, but without aligning production schedules to peak solar output, the savings were minimal. Meanwhile, aging equipment and fluctuating tariffs added to the confusion.
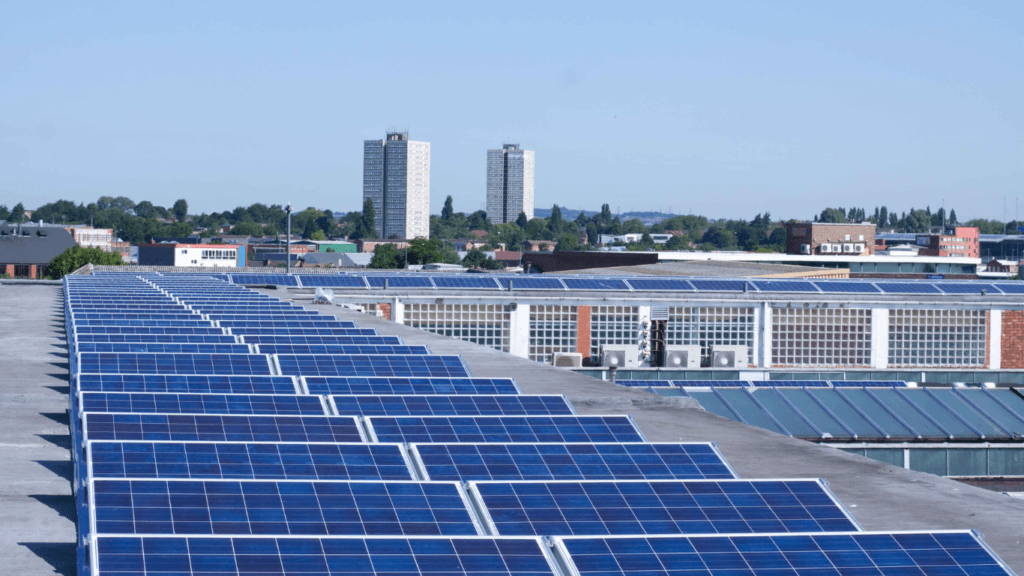
3. Vendor Overload & Unverified Promises
The energy manager, Mr. Lim, was constantly approached by vendors claiming 10–30% energy savings through different solutions: VFDs (Variable Frequency Drives), power factor correction units, AI-based energy optimization, and smart lighting systems. Each claimed to be the best, but none could provide a clear, verifiable way to measure savings in real-time.
“Every vendor had a solution, but how could I trust them? Without data, it felt like gambling with the plant’s budget,” Mr. Lim explained.
4. The Complexity of Significant Energy Users (SEUs)
Each morning, Mr. Lim reviewed energy logs, attempting to connect the dots between fluctuating consumption patterns. The chillers seemed to work harder at unexpected times, but was it due to increased production demands or inefficiencies in HVAC calibration? A particular air compressor showed spikes in energy usage—but was it a faulty valve, increased demand, or an air leak wasting resources?
Manufacturing plants are complex ecosystems where chillers, motors, pumps, and compressors interact. If a compressor is overloading, is it due to a leak? If a pump is drawing excessive power, is the motor failing? Without granular visibility, inefficiencies remain hidden.
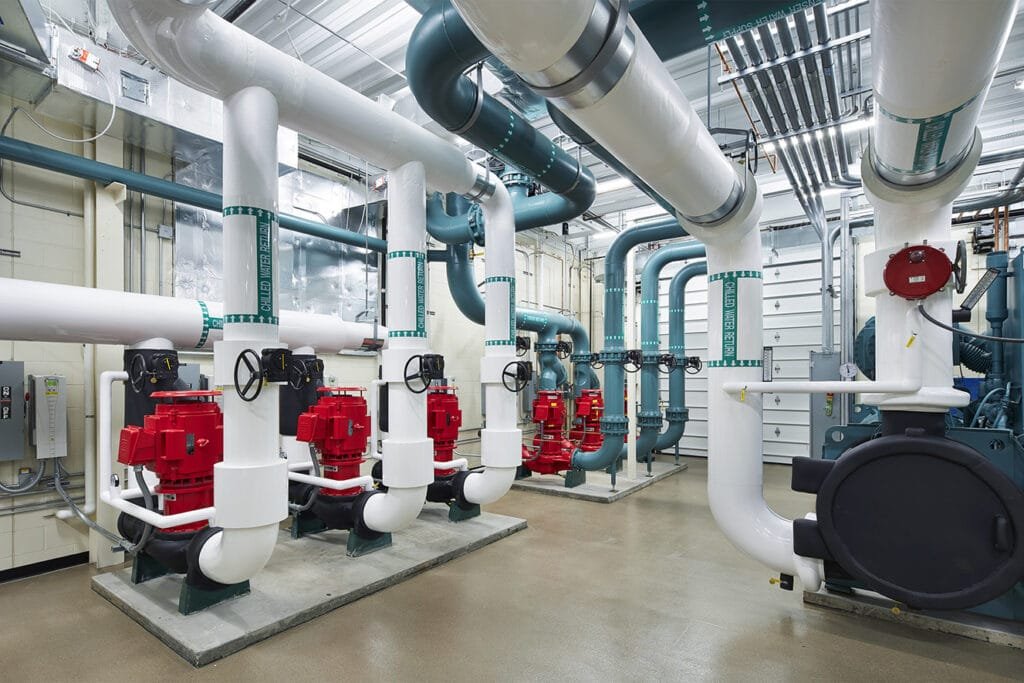
5. Compliance with EECA 2024 – The Urgent Deadline
Under EECA 2024, any facility consuming over 21,600 GJ annually must implement an Energy Management System (EnMS) and conduct energy audits. Without real-time tracking, compliance becomes a labor-intensive, guesswork-driven process.
The Turning Point: Adopting Real-Time Energy Monitoring
Juggling multiple responsibilities, Mr. Lim struggled to find time to analyze energy inefficiencies while keeping production running smoothly. Meetings with vendors, preparing compliance reports, and troubleshooting issues left him with little bandwidth for proactive energy management. Overworked and stretched thin, he knew that relying on guesswork was no longer an option. He needed a way to manage energy efficiently—without adding more work to his team’s plate.
Faced with mounting costs and uncertainty, the plant decided to implement InnoSense, an AI-powered energy monitoring platform developed by Innovast. The goal was to gain visibility into all SEUs, track energy waste in real-time, and validate vendor claims before making investments.
How the Solution Works
Step 1: Centralized, Granular Monitoring
- IoT energy meters were installed across chillers, motors, boilers, and HVAC systems.
- Data was streamed in real-time to a cloud-based dashboard, accessible from anywhere.
Step 2: Identifying the Biggest Energy Leaks
Within two weeks, the system uncovered:
- A chiller consuming 20% more energy due to a malfunctioning sensor.
- A compressed air leak leading to excessive compressor cycling, wasting RM 80,000 annually.
- Unoptimized solar usage, where power generation peaked at midday but was not aligned with energy-intensive processes.
Step 3: Vendor Accountability & ROI Tracking
- Instead of relying on generic vendor guarantees, the plant used real-time energy baselining to measure actual savings.
- When a VFD was installed on a critical motor, energy data showed a 12% reduction—validating the investment.
- Predictive alerts helped optimize energy consumption based on production schedules, further reducing energy costs by 15%.
Step 4: Compliance & Continuous Improvement
- Automated reports simplified EECA 2024 compliance, eliminating manual data entry.
- The CFO now had a clear financial case for future energy projects.
- The engineering team could focus on proactive optimizations rather than scrambling to fix unknown inefficiencies.
Addressing Common Concerns
- “What if my team isn’t tech-savvy?”
InnoSense’s intuitive dashboard requires minimal training, and Innovast provides full onboarding support. - “How much downtime is required for installation?”
The system is designed for seamless integration with minimal disruption to operations. - “What’s the ROI timeline?”
Most plants see measurable savings within the first 3–6 months, with ROI achieved in under a year.
The Results: Quantifiable Energy & Cost Savings
Within the first 6 months, the plant achieved:
RM 600,000 in annual energy savings ✅
22% reduction in peak demand charges ✅
Improved equipment lifespan due to predictive maintenance ✅
Faster, data-driven decision-making on energy investments ✅
100% EECA 2024 compliance readiness ✅
What This Means for Other Manufacturers
Innovast’s InnoSense platform ensures that energy management doesn’t become another overwhelming task for engineering teams. With automated monitoring, real-time data, and compliance-ready reports, manufacturers can focus on their core operations while meeting KPIs seamlessly.
Conclusion
For manufacturers like Mr. Lim’s plant, real-time energy monitoring is no longer a luxury—it’s a necessity. By adopting a data-driven approach, plants can uncover hidden inefficiencies, validate vendor claims, and achieve compliance with confidence.
Disclaimer: This case study is a hypothetical scenario based on specific conditions and challenges commonly faced by manufacturing plants. The solutions and results described are illustrative and may vary depending on individual circumstances.
Ready to transform your energy management? Contact Innovast today to learn how InnoSense can help you save costs, simplify compliance, and drive sustainability.